Making Interior Aircraft Parts with Additive Manufacturing
The aerospace industry has been leveraging 3D printing for numerous years and aircraft parts made with additive manufacturing provide numerous benefits. A few benefits include: contributing to weight reduction of the aircraft, detail component unitization, bill of materials (BOM) consolidation, ability to effectively scale manufacturing capacity, and applying aerospace manufacturing rigor to meet the stringent certification requirements.
Reducing Aircraft Weight
Additive manufactured aerospace parts benefit the bottom line by creating lighter-weight parts that are perfect for BOM consolidation. Interior aircraft parts such as ducting, vents and airflow systems which are made with additive manufacturing can reduce the weight of parts while having the design freedom to create shapes for parts that are more effective and efficient. Designers can incorporate flow optimization and performance enhancements into the component. These more efficient designs often allow the use of a smaller cross-section or fewer connections.
By consolidating the part count, fasteners and connections can be reduced while making the part more durable with fewer potential points of failure. Weight reduction is a performance enhancement that impacts the customer as well as the airframe integrator.
Benefits of Producing Aerospace and Defense Parts with Additive Manufacturing:
Parts Costs Reduced 50%
Scrap Reduced to 10%
Time-to-Market Reduced 64%
Part Weight Reduced 64%
Source: Deloitte
BOM Consolidation
When deciding which part to begin making with additive manufacturing, thinking beyond individual parts is key. The design freedom that comes with manufacturing production parts with an industrial 3D printer can revolutionize the way interior aircraft parts are created.
Consider a fan that is part of a cooling system, contains 73 metal parts that must be hand assembled and takes days to make just a few completed parts. This fan can be designed for additive manufacturing (DfAM) and consolidate the 73 parts down to one. This reduces assembly time, possible failure points, and hundreds of parts can be made on an industrial 3D printer in the same time it takes to hand assemble the original part
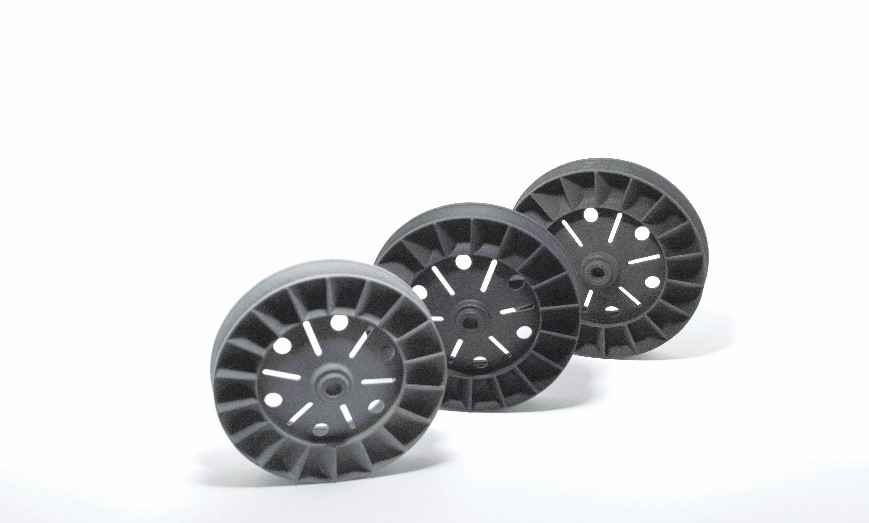
Additive Manufactured cooling fan components consolidate BOM from 73 hand-assembled parts to one AM production part.
Scalability to Support the Production Life Cycle
In addition to reducing part weight and consolidating multiple parts into one, additive manufacturing of production parts allows for easy scalability from prototype parts into full-scale manufacturing. Prototyping without the vision and expertise to eventually go into full-scale production is wasting time and money.
Leveraging expertise of additive manufacturing, design engineers at the prototype stage ensure that a product is manufacturable and will reduce the delay going from prototype to final product. These front-end considerations can also provide an end-of-life product support plan that accommodates unknown quantities and geographic distribution.
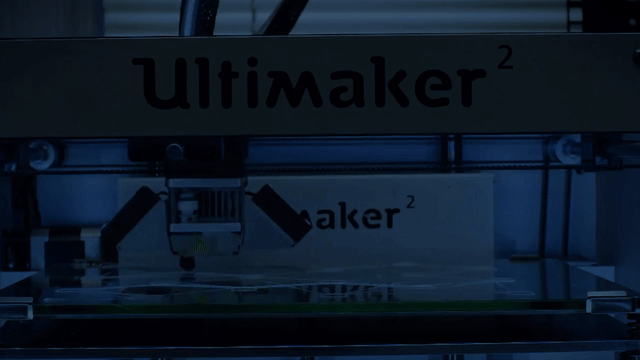
Scalability with Additive Manufacturing
Distributed Manufacturing
Once scalability has been solved for, deciding the best location to manufacture helps reduce delivery time and keeps aerospace companies competitive. Additive manufacturing can be networked across several countries and factories to produce and deliver locally.
For instance, the Jabil Additive Manufacturing Network has more than 150 3D printers networked across 27 countries. This allows customers to manufacture close to their end-users, near local factory assembly lines or customer point-of-use sites. In addition, manufacturing locally helps reduce a company’s carbon footprint, which is becoming a concern not only for the end user but also for more and more employees as they choose an employer.

Digital Thread with Additive Manufacturing
Qualification and Certification
Applying manufacturing rigor that meets industry qualification and certification is a must for the aerospace industry. This same manufacturing rigor needs to be applied when leveraging industrial 3D printers to create production parts. Materials, Processes and Machines (MPM) must all meet industry certification and be created in an ISO 9001 facility, while the components themselves need to be produced in an AS9100 compliant facility.
Engineered additive manufacturing materials provide the durability, tensile strength and characteristics that are needed within the aerospace industry. These custom materials can have flame retardant, conductive properties or mechanical enhancement and can be used to broaden the applications to part types that were previously not considered due to their design requirements. However, to ensure consistency, these additive manufactured materials must be created in an ISO 9001 facility with controlled processes. This will ensure how each material will react, once it becomes a part, based on which industrial 3D printer on which it was manufactured. With the strides that the additive manufacturing industry has made over recent years, this is now becoming a necessity for any production part made with additive manufacturing.
What to Make and Why
It’s very clear that an aircraft is a complicated system that involves a long list of interior and exterior parts to keep it safe, certified, functioning, comfortable and cost-effective. Interior components are ideal for additive manufacturing. Ducts, vents and air flow components are perfect candidates due to the high complexity and likely BOM consolidation as well as the ability to improve the structural efficiency.
In addition, leveraging DfAM skillsets enables these parts to support compact packaging by better utilizing the available volume within a confined space. Designing additive manufactured parts that are printed instead of injection-molded or manufactured using a CNC machine creates endless possibilities with interior aircraft parts. Positioning features and subtly changed replicant designs do not add additional tooling cost, rather it is a simply a second part number that can further optimize system performance rather than utilize the best average design. Internal channels or angles that previously had to be assembled can now be integrated for a streamlined manufacturing process.

Aerospace Additive Manufacturing
Impacts of Additive Manufacturing for the Aerospace Industry
Additive manufacturing is an enabling technology that gives aerospace companies the ability to continue to push existing boundaries through creative use of the available volume with the least amount of required material. This is a competitive advantage that allows companies to better position themselves for longevity in a highly competitive market.
Moving Forward with the Additive Manufacturing of Aerospace Parts
Aerospace companies should consider partners who can help support the expansion of their business of manufacturing high-performance air vehicles. In addition, a partner to an aerospace company needs to understand how to seamlessly merge traditional and additive manufacturing together while being able to quickly scale manufacturing capabilities that meet qualification and certification standards.