The Future of 3D Printing: Five Predictions
What can be done with 3D printing isn’t theoretical anymore. It’s now a manufacturing imperative.
Just a few years ago, the benefits of additive manufacturing remained speculative. We were debating whether there was a financial or technological case to convert from traditional, high-volume processes to additive processes. Now, the demonstrable time-savings in design and manufacturing along with higher efficacy products are leading to a rapidly growing number of use-cases, positioning 3D printing as a mainstream manufacturing technology. Additive manufacturing has found its stride, and as an increasingly important pillar in the manufacturing renaissance, the future of 3D printing is bright.
Numerous industries—including healthcare, aerospace and defense—have been experiencing transformations within key areas of their business that can be attributed to the expanded digital infrastructure, materials development and supply chain maturation, and greater stability within additive manufacturing technologies.
In aerospace, making interior aircraft parts like ducting, vents and airflow systems with additive manufacturing permits designers to trim weight, reduce the number of components in assemblies, conform to tight cabin interiors. In addition, 3D printing provides the design freedom to experiment with more effective and efficient part shapes, with fewer potential points of failure improving the management of a sensitive thermal environment. As product development cycles shrink across every industry, these capabilities give manufacturers a level of design, production and supply chain flexibility previously unobtainable.
In Jabil’s third biennial 3D Printing Trends survey, we discovered that the variety of additive manufacturing applications have diversified dramatically in the last two years. In fact, research and development overtook prototyping as the top use case, while use cases for jigs, fixtures and tooling jumped from 37% in 2019 to 57% this year. We also saw a sharp increase in the percentage of companies using 3D printing for bridge production, growing from 39% to 56% in just two years. Finally, more than six in 10 now use 3D printing for production parts.
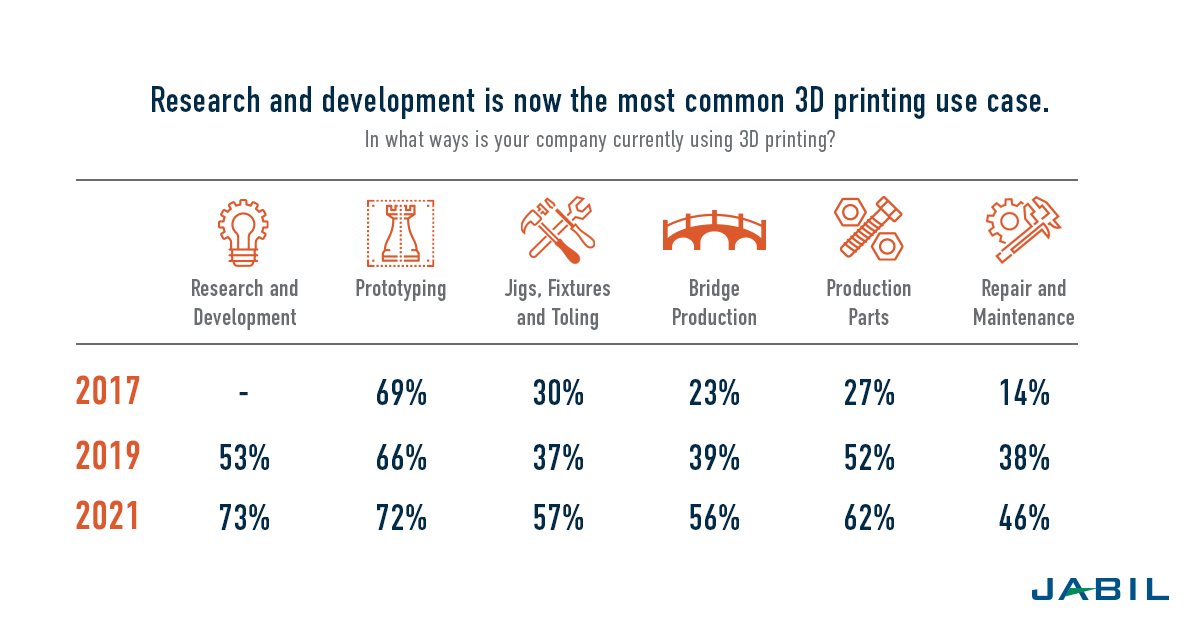
When asked how their company’s top leadership viewed 3D printing, more than half responded that they considered it a “strategic capability.” Given leadership’s tendency to look at the bigger picture, there are big considerations at play for the future of 3D printing. But as additive manufacturing technology adoption grows, how will it shape other industries and aspects of manufacturing? What does the future of 3D printing hold? Here are five predictions.
1. Scalability from Rapid Prototyping to Production
3D printing use for jigs, fixtures and tooling, bridge production and production parts have grown remarkably over the last few years. In that time, the heavy equipment and industrial machines industries have seen the highest adoption of use cases for jigs, fixtures and tooling; healthcare has been the biggest adopter of bridge production; and the orthopedics and industrial machines industries have seen the highest adoption rates in using 3D printing for production parts.
Additive manufacturing benefits every step of the product development process, enabling easy scalability in rapid prototyping to full-scale manufacturing. After all, prototyping without an eye for full-scale production misses a key tenant of what additive stands to deliver: more efficient lifecycle management.
When volumes are still relatively low – if a brand is looking to print 100 parts for testing or regional-market testing – additive manufacturing enables a team to iterate on designs and features free of charge. Even quadrupling that number can be done with no added retooling costs using 3D printing.
Additive remains the perfect fit for low- to mid-volume production where high tooling costs and high fixed costs can deter market entry. With the right level of planning, engineering and material development, 3D-printed parts can seamlessly transition into rate production equipment, such as injection molding.
Producing a part on-demand enables manufacturers to produce 3D printed parts as needed instead of pulling the part from a supply warehouse. On-demand production leads to measurable reductions in inventory and storage costs. In the automotive industry, spare parts inventory can be reduced by 90% with 3D printing, according to a report from MIT.
In shipbuilding, transitioning the production of certain parts from traditional methods to additive has proven to deliver attractive returns. For a metal part that averaged a 12-week turnaround and an average cost of $20,000 using traditional methods, using 3D printing to produce the same part decreased production time to less than 72 hours at a cost of $1,250, according to research from Gdynia Maritime University in Poland.
Today, we’re moving from a capability conversation to capacity conversation. In the future, 3D printing application opportunities will be increasingly integrated into all facets of new product introduction (NPI) where scaling volume to achieve price points will become decreasingly important.
2. Making the Supply Chain More Resilient Through Digitization
If the global pandemic has taught us anything, it’s that global supply chains can be unpredictable. Historically, supply chain management has focused on cost and efficiencies at the expense of resiliency. It’s no wonder that many supply chains failed when faced with a disruption as big as the pandemic—COVID-19's supply chain impact was felt across every industry, but especially in healthcare and medical devices. Now, building supply chain resilience is a key objective across industries.
When a shortage of personal protective equipment (PPE) and ventilator parts was crippling the healthcare supply chain, additive manufacturing was a big part of the solution. Faced with pandemic-related obstacles, Superfeet, an insole manufacturer, dedicated available capacity to producing face shields. With 3D printing serving as their main manufacturing method, converting their lines to produce shields was done quickly with little switching cost.
In addition to supporting the production of face shields and masks, 3D printing led to innovations in ventilator parts that helped save lives. For example, Jabil supported the rapid development of ventilator splitters that allowed one ventilator to be used for several patients at once. With additive manufacturing, we were able to produce more than 60,000 splitters in just three weeks with the requisite level of quality to ensure positive patient outcomes.
It’s no surprise that additive manufacturing is a leading factor in digital transformation. It’s one of the purest digital technologies because it doesn’t require tooling and fixturing, thereby reducing or eliminating switching costs in moving production between different printers and locations. That’s a radical departure from labor-intensive methods employed by the manufacturing industry over the last 150 years where aggregation of high volume at a single site was required to achieve cost targets, especially in the highly price-sensitive consumer product markets.
In fact, the most disruptive aspect of additive has little to do with the actual printers—it’s the conversion of a digital form into a physical good, meaning a file that has a representation of the final product as opposed to a design that may compromise “product intent” to adhere to the traditional manufacturing process. 3D printing is the first step on the digital transformation journey.
Rather than stocking a warehouse full of components that might become obsolete and mass quantities of spare parts that may or may not be in demand, additive manufacturing condenses the piles of boxes eating up physical space into digital files that can be stored in the Cloud and easily accessed when needed.
In addition to digital inventories, the ability to distribute manufacturing is also changing how companies are incorporating the 3D printing process into their product strategies. Instead of solely considering a centralized solution given historically prevalent economic paradigms, distributed manufacturing enables companies to decentralize production so they can manufacture the final product closer to the customer. For example, the Jabil Additive Manufacturing Network fuels a growing 3D printer network and additive manufacturing capabilities to move manufacturing workloads to the most ideal geographic markets with speed and agility to deliver the lowest landed costs at lot sizes appropriate for the product and market.
With 3D printing, manufacturers can better connect the physical supply chain with a digital thread and manage products more efficiently from concept to end-of-life. Manufacturing can be distributed to any location that has digital manufacturing systems in place simply by putting a file on the wire. This decentralization increases transparency and collaboration. If another global event like a pandemic causes gridlock in the supply chain, additive manufacturing will be increasingly positioned to react, enabling companies to move forward more seamlessly than with a strict reliance on traditional manufacturing.
The future of additive manufacturing entails a hybrid version of manufacturing that includes a reduced number of large mega-factories, with smaller sites including more digital technologies, such as 3D printing, gaining prominence. It is also expected that printers will more commonly be deployed in non-traditional locations, like service and support centers, distribution centers or even in people’s homes to attend to the “Last Mile” of product distribution.
3D printing will eventually become simple enough that most households will be able to purchase brand files and print a product with just a few clicks, like 2D printing at Kinko’s a mere decade ago. We’re already on this course, and we’re just beginning to distribute closer to consumption delivering the levels of agility consumers have come to expect from other marketplace disruptions created by companies such as Google and Amazon around information and shopping.
3. Offering Greater Flexibility and More Customized Designs
A prevailing consumer trend transforming numerous industries is the desire for customized products. Rather than purchasing an item that was made through mass production, customers are more frequently wanting a product that is created for them specifically, gratifying their personal tastes and preferences.
Personalization and customization can be easily enabled with the low-volume production capabilities offered by additive manufacturing. 3D printing gives brands more flexibility in responsive design, specifically through design for additive manufacturing. Instead of making advanced market predictions and then spraying large quantities of identical objects into the market, manufacturers can afford to produce smaller batches, allowing designers and engineers to adjust product designs and innovate in a cost-effective manner as inspiration strikes, consumer sentiment is known, or customer feedback trickles in.
The accessibility of 3D printing is starting to reach the point where you wonder, “what can’t we print?” And when we start to dissect everything down to the molecular level, it’s just a matter of time before individual consumers can print food or frames for their glasses or… well, anything. In the future, 3D printing and future permutations of digital production will more fully empower consumers.
4. The Future of Digital is all about Materials
While increasing investments in the additive manufacturing ecosystem are fueling growth, I don’t think you can overstate the significance of the materials. Outside of the high cost of the equipment, the next big barrier is materials and closed additive manufacturing ecosystems, which have stymied the 3D printing industry’s growth. Numerous types of 3D printing materials are on the market today, but few are advanced enough to meet the quality or regulatory requirements of industries.
With current challenges surrounding volumes in most industries, suppliers and manufacturers aren’t incentivized to create the different materials necessary for new applications. However, the future of 3D printing is in materials—specifically engineered and application specific materials. The different needs of diverse industries all require custom solutions to their problems. Integrating new engineered materials will transform a new generation of applications, including heavily regulated industries.
The markets will reward companies that compress the process and timeline associated with introducing 3D printing materials tailored to specific manufacturing and engineering requirements. By establishing the processes to accelerate the development and release of materials into the additive markets in a cost-effective manner, a greater number of 3D printing applications will be served and the overall digital manufacturing flywheel will begin to spin.

Jabil Engineered Materials
5. Creating a More Sustainable Future with 3D Printing
Finally, two of the key tenets to additive manufacturing are sustainability and conservation. One of the intrinsic benefits is that scrap material is reduced, if not eliminated. As Simon Ford and Mélanie Despeisse point out in their essay, “Additive Manufacturing and Sustainability: An Exploratory Study of the Advantages and Challenges,” additive manufacturing mimics biological processes by creating objects layer by layer, rather than produce a hulking item that must be whittled and chunks carved out to achieve the desired shape. “It is inherently less wasteful than traditional subtractive methods of production and holds the potential to decouple social and economic value creation from the environmental impact of business activities,” they write.
Aside from reducing waste, 3D printing also conserves energy. The Metal Powder Industries Federation did a study that listed 17 steps required to produce a truck gear using subtractive manufacturing versus the six steps to manufacture the same product with additive manufacturing. With 3D printing, the same product took less than half the energy. Additionally, by bringing products closer to the customer, 3D printing reduces the need for transporting products and materials, thereby positively affecting the quantity of carbon poured into the atmosphere. Therefore, we can already see that digital and additive strategies are already leading to a more sustainable future.
This is a pivotal time for the manufacturing industry. We’re standing at an epicenter where our ideas, designs and products can be nearly fully represented in the digital space and we can increasingly convert those representations into physical products using sound production methods cost-effectively with appropriate quantities using additive. As the first truly digital production technology, additive manufacturing is demonstrating its transformative nature and has already been reshaping businesses and industries with remarkable efficiencies.
How do you expect your company's use of 3D printing to change in the coming 2-5 years? Choose the answer that most closely applies.
According to our survey, 87% of companies expect their use of 3D printing to at least double, and nearly 40% expect their usage to increase five times or more. As we adopt additive manufacturing, companies will be able to reduce batch sizes, realize faster NPI and development and, ultimately, where the cost curves intersect, use it as a full serial production tool. We are laying a foundation to enable distributive manufacturing to deliver more innovative products, improve user-experiences and better patient outcomes. It doesn’t take a crystal ball to see that the future of 3D printing is bright.
Download the 3D Printing Technology Trends Report
Jabil's third biennial report includes insights from over 300 individuals responsible for decisions around 3D printing at manufacturing companies on technology adoption, opportunities and challenges.
Jabil Additive Manufacturing
Click 'Learn More' to explore all of Jabil's Additive Solutions.