Top 3D Printing Challenges (And How to Overcome Them)
The outlook for 3D printing is exceedingly positive—nearly every report published in the last decade explores the potential of additive manufacturing and how it can help transform parts of the manufacturing process. The optimism is well-placed. The technology has experienced unprecedented growth in the last several years. But it would be naïve to overlook the biggest 3D printing challenges and how they shift as the technology evolves.
Since 2017, Jabil has surveyed over 300 product brands about their 3D printing capabilities, adoption, as well as current challenges and future plans. In the time since our first survey, additive manufacturing has come a long way—discussions of potential benefits have translated into real business outcomes that promise potential across every industry. For example:
- At Jabil's Auburn Hills site, using 3D printing for jigs and fixtures has led to a time reduction of 80% (from months to weeks) and up to 30% reduction in tooling costs.
- With additive manufacturing, a fan within an aircraft cooling system can be consolidated from 73 labor-intensive and time-consuming parts to one.
- Using 3D printing, HP saw breakeven points for production parts climb from 5,000 units up to 40,000 units.
- Traditionally-machined manifolds in medical devices can be significantly simplified with the 3D printing process.
These proof points highlight the transformative impact of additive manufacturing. While many product brands have seen tremendous time- and cost-savings in everything from prototyping, design and production parts, others are waiting for the technology to be ready for use in their industry.
Regardless, 94% of survey participants admit to facing 3D printing challenges. Those challenges have shifted over the last few years, showcasing the advancements in the technology to production readiness, which unveils new obstacles to overcome.
Download Jabil's 2021 3D Printing Technology Trends survey report.
Critical 3D Printing Problems and Solutions
In the 2017 survey, respondents indicated that their biggest additive manufacturing challenges were related to costs (of pre- and post-processing, system equipment and materials), whereas 2019 respondents found 3D printing material issues to be most challenging. Today, however, challenges seem to vary: the cost of pre- and post-processing, the limited selection of materials and technology limitations are the biggest 3D printing challenges of 2021.
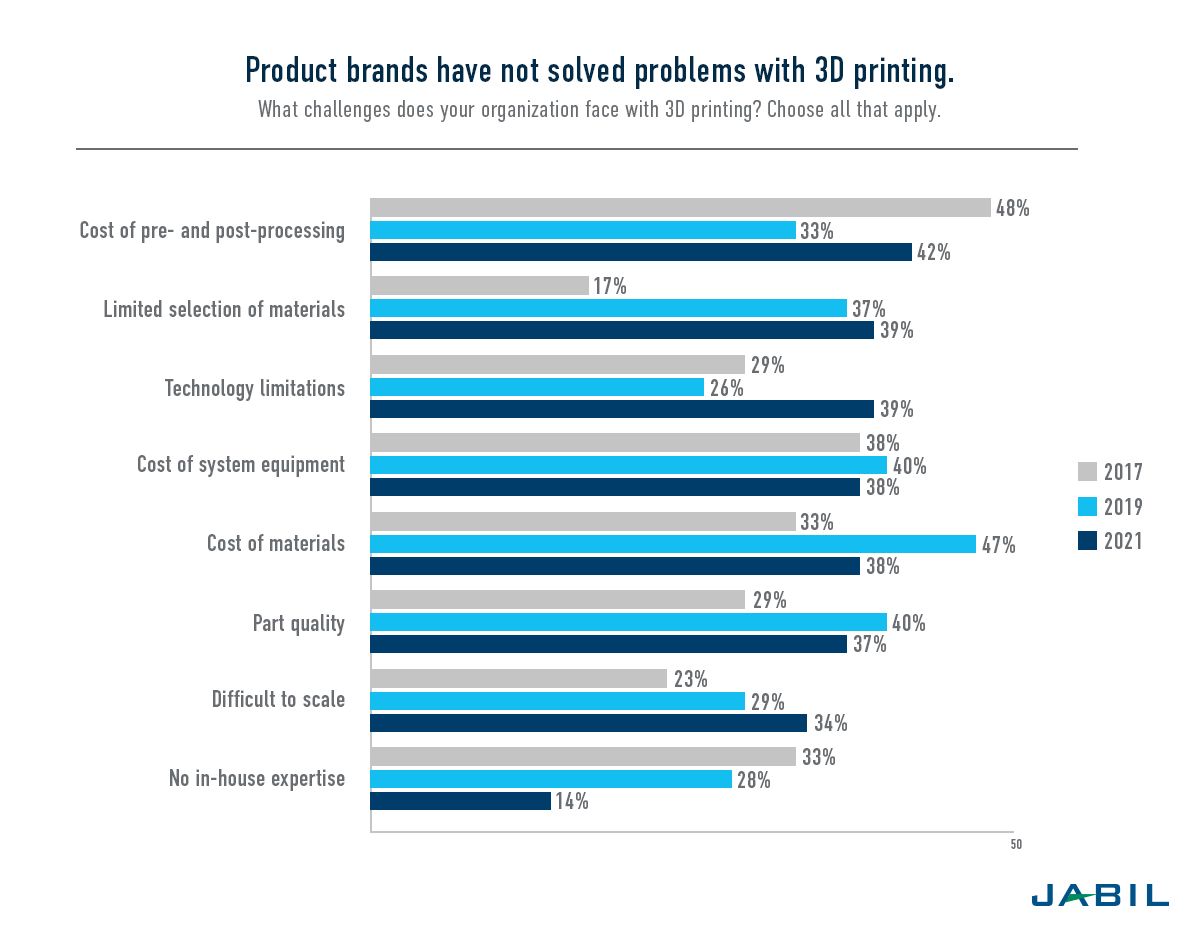
3D Printing Challenges in 2021
Although these 3D printing problems represent the top challenges faced across industries such as consumer electronics, healthcare, heavy equipment, automotive, industrial machines and packaging, there are some small differences when we examine the details by industry.
Consumer Electronics | Healthcare | Heavy Equipment |
1. Cost of pre- and post-processing |
1. Limited material selection 2. Cost of pre- and post-processing 3. Cost of system equipment |
1. Cost of pre- and post-processing 2. Cost of materials 3. Limited material selection |
Automotive | Industrial Machines | Plastics & Packaging |
1. Limited material selection 2. Cost of pre- and post-processing 3. Technology limitations |
1. Cost of pre- and post-processing 2. No in-house expertise 3. Cost of system equipment |
1. Limited material selection 2. Cost of pre- and post-processing 3. Technology limitations |
According to Jabil's survey results, the cost of pre- and post-processing is the top challenge for the consumer electronics, heavy equipment and industrial machines industries, whereas healthcare, automotive and packaging industries are most likely to struggle with the limited selection of materials.
Diving deeper into what prevents product brands from using 3D printing in mass production today, 54% say materials issues (cost or availability of materials) are number one. Another 43% highlight their workforce issues (such as the lack of qualified personnel or subject matter experts). Finally, 42% affirm facing platform issues (availability or cost of 3D printers) and process issues (design or post-processing issues).
While the mentioned challenges have stayed mostly steady over the last two years, there is a notable exception: ecosystem issues, which rose by 13% from 2019 to 2021. This could be due—at least in some part—to the vulnerabilities revealed by the supply chain impact of COVID-19. Companies across all industries were forced to evaluate the speed and agility of their operational processes as well as how smoothly everything works together.
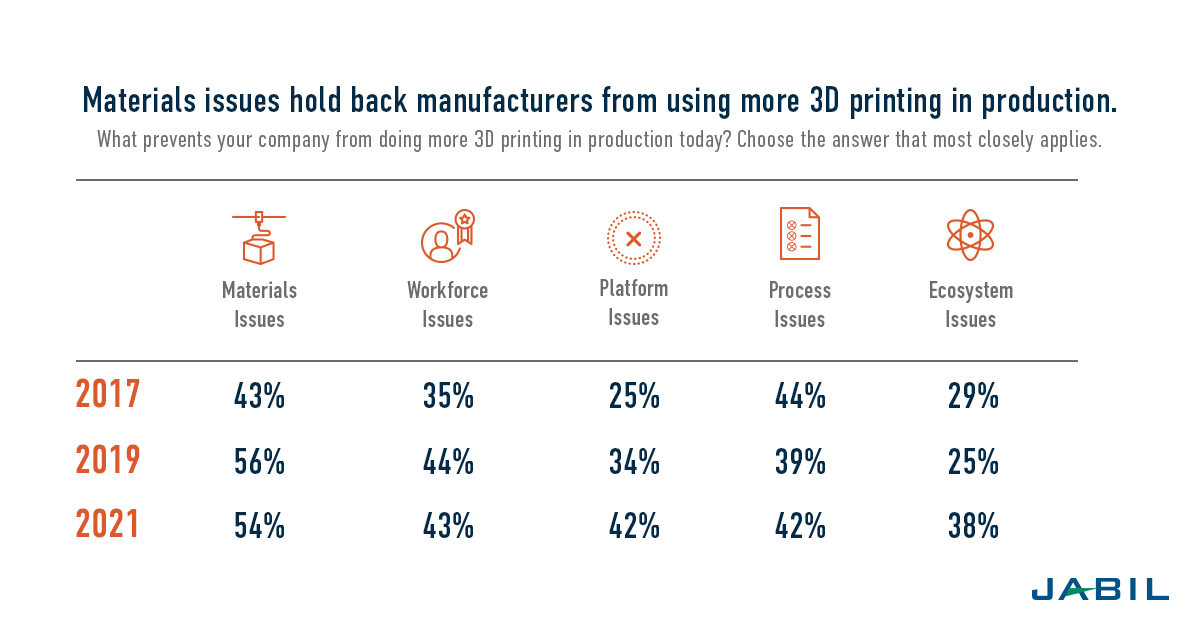
3D Printing Challenges in Production
Navigating Challenges with Additive Manufacturing Materials
In the 2019 survey, 94% said that their design and engineering teams frequently choose traditional manufacturing methods over additive manufacturing due to a lack of materials. It makes sense. The cost and availability of 3D printing materials may be the main obstacles, but material performance is a significant barrier.
As I mentioned earlier, part quality—integrity, strength, aesthetics, etc.—is a challenge many manufacturers face. While some sectors are doing well and transforming their customer experiences (for example, the dental and hearing aid industries), others haven't yet moved beyond prototyping to part production. This is because certain industries (such as healthcare and aerospace) require certified materials or specific qualifications for the materials to be used beyond prototyping.
According to the Jabil survey, polymers are the most commonly used 3D printing materials today, but participants are most interested in using metals next. Currently, 3D printing is most suitable for complex, bespoke parts that are costly and difficult to produce via traditional methods. But as advancement are made in lowering the cost of materials and faster machine throughput, metals for additive manufacturing use will be much more accessible to product brands.
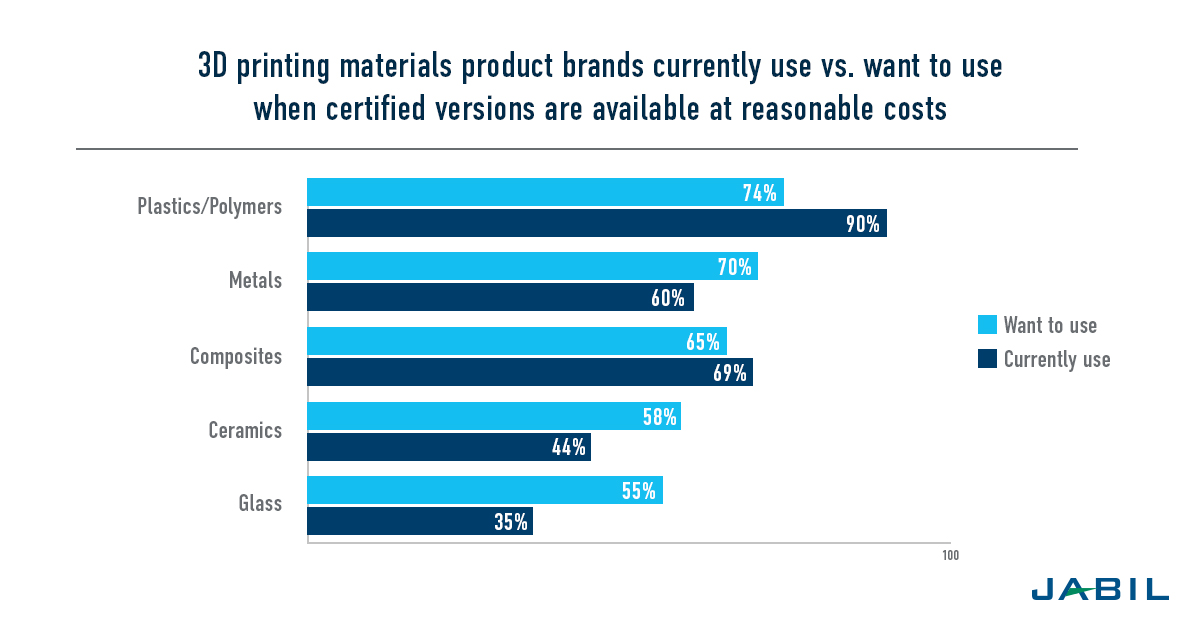
3D Printing Materials Product Brands Currently Use vs What They Want to Use in the Future
When considering which additive manufacturing materials to use, keep custom engineered materials in mind. Through engineered materials, product brands can access custom powders and filaments, with manufacturing rigor applied to each specialized material. This way, your part performance and requirements match perfectly. Greater availability of unique materials, a shorter time-to-market and reduced costs on part development are just some of the benefits of using custom materials.
Considering that additive manufacturing technology has come a long way in the last few years, I don't expect material challenges to last much longer. As new materials are introduced, our ability to produce 3D printed parts that meet our expectations will be strengthened. Since the 3D printing technology can also enable us to consolidate the number of parts we use, the opportunities are just waiting to be seized.
Six out of 10 survey respondents said that when a greater variety of cost-effective, certified additive materials are available, they will increase the types of applications that utilize 3D printing. In addition, 59% say they will 3D print more production parts.
Budgetary Limitations in Additive Manufacturing
Manufacturers need a reliable additive manufacturing system that can offer the quality they expect and promise from their operations. But quality comes at a cost. Therefore, it is not surprising to see the costs of system equipment and materials to be reported as a barrier in 3D printing adoption.
Before taking on additive manufacturing as a practice, you must first develop your strategy. Analyze your supply chains and parts you produce, develop a business case and make it all part of your strategy with a budget. Additive manufacturing is a long-term investment for your organization, if not a complete manufacturing transformation. Although the systems and materials may seem costly, they may offset or lead to significant cost-savings in productivity, efficiency as well as part and mechanical property.
For those who don't want to take on 3D printing in their own supply chains, working with an external partner (like Jabil) is always another option. In fact, almost half of survey participants say outsourcing will be a significant part of their future plans for 3D printing.
Addressing the Lack of In-House 3D Printing Expertise
Considering how fast additive manufacturing is advancing, it can be very difficult to find the right talent to grow the technology in your organization, as indicated in the survey results.
The reality is that you can draw on your team members. Whether it is injection molding or design, you can cross-train your existing talent to get them up to speed with 3D printing. Your design teams may require more support as they learn to design for additive manufacturing. Companies that focus on training their teams on using the technology see positive benefits such as a more excited team, increased creativity and pride of workmanship, according to the survey.
As your designers and engineers have gained experience with additive manufacturing, how have they reacted?
As is with any other case, investing in your experienced and incoming talent will be key to overcoming this challenge. In addition, your organization may want to consider partnership opportunities with universities that have already launched 3D printing labs to deliver training to engineering students.
Whether you are new to additive manufacturing or mature in your use of it, the competition for skilled talent will not be an easy one.
Opportunities to Advance 3D Printing Technology to Scale Operations
One of the primary attributes you can use to differentiate your business on is speed. Speed to concept, speed to prototype and speed to production are what matter in this world of instant gratification. Additive manufacturing is set to meet these demands as the technology advances.
Ultimately, 3D printing reduces the barriers to get a product to market or do a test market, as it doesn't require the significant investments in tools, molding and equipment required with traditional manufacturing methods. Organizations from startups to multi-national companies can all benefit from additive manufacturing.
Partnerships in the industry are already leading to big results and bringing additive manufacturing much closer to production for several industries. As the technologies become more open, innovation will thrive.
Product Brands are Optimistic About 3D Printing Problems and Solutions
The good news is that 98% of respondents were optimistic that we'll be able to overcome challenges surrounding additive manufacturing. In fact, 55% expect these challenges to be overcome as soon as the next three years.
We will need to focus our energy on the following to overcome these challenges:
- Strategy development
- Hiring and training
- Monetary investments
- New technology and innovation in additive manufacturing
- Time to change the production process and attitudes
The one element we haven't focused much on is time. While manufacturers haven't always been known to embrace change, we live in a world where change is constant. Now is the time for manufacturers to prove how they handle change management.
Download the 3D Printing Technology Trends Report
Jabil's third biennial report includes insights from over 300 individuals responsible for decisions around 3D printing at manufacturing companies on technology adoption, opportunities and challenges.